Check Valve
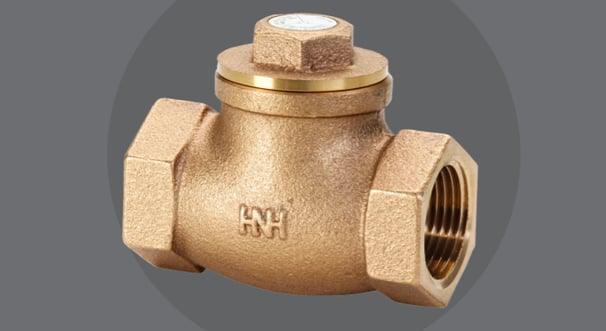
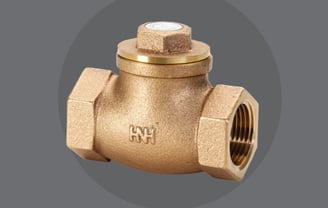
1. Types of Check Valves
a. Swing Check Valves:
Design: Utilizes a disc that swings on a hinge to allow forward flow and close against backflow.
Applications: Commonly used in water and wastewater systems, fire protection systems, and HVAC.
b. Lift Check Valves:
Operation: Features a disc that lifts off the seat to allow flow and drops back down to prevent backflow.
Advantages: Suitable for vertical or horizontal applications, offering better sealing in high-pressure systems.
c. Dual Plate Check Valves:
Design: Consists of two plates that pivot on a central pin, providing a quick response to changes in flow direction.
Applications: Often used in high-flow and high-pressure systems, including oil and gas pipelines.
d. Ball Check Valves:
Operation: A ball sits in a seat and allows flow when pressure is applied; it drops back to seal the opening when flow reverses.
Uses: Ideal for low-pressure applications, such as in water and sewage systems.
e. Wafer Check Valves:
Design: Compact design that fits between flanges, making them suitable for tight spaces.
Applications: Used in various industries for fluid handling.
2. Material Specifications
Common Materials:
Body Materials:
Stainless Steel: Offers excellent corrosion resistance, suitable for aggressive environments.
Carbon Steel: Cost-effective for standard applications.
PVC or CPVC: Used for chemical applications where metal may corrode.
Seals and Seats:
PTFE: Chemical resistance for various applications.
Rubber or EPDM: Good sealing properties for general applications.
3. Size and Dimensions
Diameter:
Available Sizes: Typically ranges from 1/2 inch to 24 inches or larger based on client requirements.
Body Style:
Configurations: Available in flanged, threaded, or welded designs for integration into existing systems.
4. Pressure Ratings
Typical Ratings: Manufactured to meet various pressure ratings, commonly including:
150#, 300#, 600#, or as per client specifications.
Set Pressure Range: Customizable to meet specific application needs.
5. End Connections
Connection Types:
Threaded Connections: Standard for smaller valves.
Flanged Connections: Common for larger valves, ensuring secure attachment.
Welded Connections: Used for permanent installations.
6. Operating Mechanism
Automatic Operation:
Flow Direction: Opens to allow fluid flow in one direction and closes automatically to prevent backflow.
Spring-Assisted Designs:
Improved Performance: Some models include a spring mechanism to ensure quick closure and prevent slamming.
7. Special Features
Low Pressure Drop:
Efficiency: Designed to minimize pressure loss across the valve.
Corrosion-Resistant Coatings:
Durability: Optional coatings enhance performance in corrosive environments.
Testing Ports:
Convenience: Allows for pressure testing without dismantling the valve.
8. Testing and Certification
Testing Protocols:
Hydrostatic Testing: Ensures the valve can withstand high pressure without leakage.
Performance Testing: Verifies that the valve opens and closes effectively in response to flow direction changes.
Certification:
Compliance Standards: Adheres to ASME, API, and other relevant standards.
9. Documentation
Technical Data Sheets:
Specifications: Provide detailed information on materials, pressure ratings, and performance characteristics.
Material Certificates:
Compliance: Documentation certifying that materials meet specified standards.
Inspection Reports:
Quality Assurance: Detailed reports on testing results and certification.
User Manuals:
Guidance: Instructions for installation, operation, and maintenance of the check valves.
QUALITY
Supplying High-Quality Plates, Wire Mesh, perforated Sheets, Coils, All types of Flanges, Round Bars, Fasteners, Vales, Strainers etc.
Contact us
Request a quote
✉️ Email:
admin@mw-enterprises.com
abdulwahab.ansari@mw-enterprises.com
📞 Phone: +91 90281 70158
MW Enterprises © 2024. All rights reserved. Developed by Nirav Chauhan
Our sales & supply are in below countries:
Saudi Arabia, Qatar, Oman, Kuwait, United Arab Emirates (UAE), Dubai, Bahrain, Italy, Indonesia, Malaysia, Jordan, Sri Lanka, Vietnam, South Africa
Abdul Wahab Ansari
MW Enterprises General Trading Company