Needle Valves
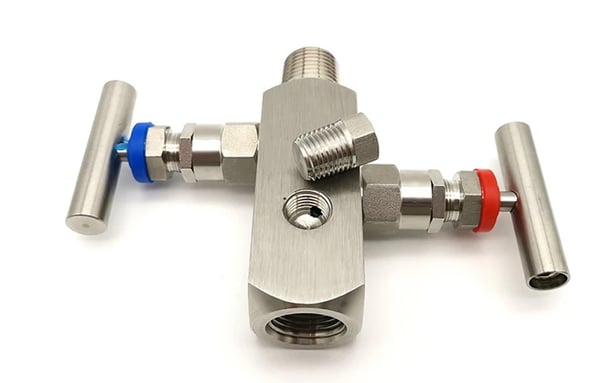
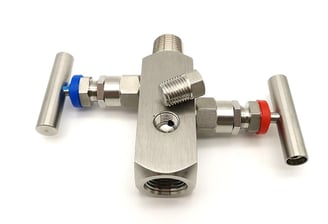
1. Size Range:
Typically available in sizes from 1/8" to 2" (DN 6 to DN 50).
2. Pressure Ratings:
Pressure ratings vary from 6,000 PSI to 20,000 PSI (414 bar to 1,379 bar) depending on the material and design.
High-pressure models can handle pressures up to 60,000 PSI.
3. Material Specifications:
Stainless Steel: SS 304, SS 304L, SS 316, SS 316L
Carbon Steel: ASTM A105
Alloy Steel: Inconel, Monel, Hastelloy
Brass
Duplex Stainless Steel: F51, F53, F55
Other Materials: Copper, Nickel, Titanium (for specialized applications)
4. End Connections:
Threaded: NPT, BSPT, BSPP (1/8" to 2")
Socket Weld
Butt Weld
Compression Fittings
Flanged Ends: ASME/ANSI, DIN, EN standards (for larger sizes)
5. Temperature Ratings:
Needle valves can operate within a wide temperature range, typically from -20°C to 450°C, depending on the material and application.
Special high-temperature versions are available for temperatures up to 650°C.
6. Design and Features:
Bonnet Design: Integral bonnet or union bonnet designs to suit the pressure requirements.
Stem Types: Non-rotating stem, rising stem, or rotating stem.
Packing Options: PTFE, Graphite, or other materials based on temperature and pressure requirements.
Metal-to-Metal Seating: Ensures high sealing efficiency and durability.
Soft Sealing: For applications where a bubble-tight seal is required, soft seats made of PTFE or PEEK are used.
Handle Types: T-handle or round handle, made from materials like plastic, aluminum, or stainless steel.
7. Applications:
Flow Control: Used for fine adjustment of flow in instrumentation lines, gas or liquid pipelines, and high-pressure applications.
Isolation: Often used in isolation for sampling, pressure measurement, and calibration lines.
8. Standards & Certifications:
Manufacturing Standards: ASME B16.34, API 602, ISO 5208.
Certifications: Fire-safe, API 607, ISO 10497, CRN, and NACE MR0175 compliance for corrosion resistance in harsh environments.
Testing: Hydrostatic testing, seat leakage testing, and helium leak testing.
QUALITY
Supplying High-Quality Plates, Wire Mesh, perforated Sheets, Coils, All types of Flanges, Round Bars, Fasteners, Vales, Strainers etc.
Contact us
Request a quote
✉️ Email:
admin@mw-enterprises.com
abdulwahab.ansari@mw-enterprises.com
📞 Phone: +91 90281 70158
MW Enterprises © 2024. All rights reserved. Developed by Nirav Chauhan
Our sales & supply are in below countries:
Saudi Arabia, Qatar, Oman, Kuwait, United Arab Emirates (UAE), Dubai, Bahrain, Italy, Indonesia, Malaysia, Jordan, Sri Lanka, Vietnam, South Africa
Abdul Wahab Ansari
MW Enterprises General Trading Company